Introduction to Cooking Oil Recycling
Cooking oil recycling is now a cornerstone of the transportation sector, turning fryer drippings into a renewable energy source that keeps trucks rolling without leaning on new fossil fuels. Every week, millions of gallons of used cooking oil leave kitchens, flow through sealed pipes, and come back as low‑carbon biodiesel fuel that moves effortlessly through standard fuel lines in any modern diesel engine. Swapping petroleum diesel for biodiesel or renewable diesel cuts greenhouse gas emissions by up to 78 percent—something conventional diesel has never achieved.
The heart of the transformation is a chemical process called transesterification. Technicians blend filtered oil; typically vegetable oil such as canola oil, soybean oil, or rendered animal fats; with methanol and precise amounts of sodium hydroxide and potassium hydroxide. This reaction splits triglycerides so the oil produces two streams: an upper flow of methyl esters that make biodiesel and a lower glycerol layer sold for animal feed. Each batch adds to the five‑billion‑plus gallons of biodiesel produced in the United States every year.
Restaurants famous for fried food—from crispy fried chicken to heaping plates of French fries—now see fryer oil as an asset rather than a headache. Capturing that hot oil diverts waste vegetable oil, used oil, and kitchen grease away from the sewer system.
Cooking Oil Collection and Transportation
Effective cooking oil collection begins at the fryer. Line crews oil regularly filter the vats and drain the used fryer oil into sealed totes, straining out food scraps, food particles, and excess moisture. Licensed haulers, working under strict local regulations, pump the load into vacuum trucks. Onboard screens pull out the last bits of unfiltered oil, so every gallon reaches the recycling facility ready for processing.
Haulers also service grocery stores, stadiums, and university dining halls—any site with large fryers. Pickup logs satisfy municipal FOG rules. At the depot, a rapid filtration process; 200‑micron screen, low‑heat settling, and centrifuge—prepares the oil in a few hours so plants can quickly produce biodiesel.
Grease Traps, Sewer Lines, and Preventive Maintenance
Well‑maintained grease traps are the first defense in cooking oil recycling. Under the “twenty‑five percent rule,” crews pump traps when the grease and sludge layer reaches one‑quarter depth. Timely service shields every downstream sewer line, stops fatbergs, and saves restaurants from surprise plumbing bills. Reliable grease trap routines also prevent hydrogen‑sulfide corrosion that lets waste oil seep into waterways.
City inspectors monitor grease traps closely. Kitchens that maintain them enjoy smoother pickups and fewer fines, proving that steady grease trap service underpins the entire oil‑to‑fuel chain.
From Waste Oil to Fuel—The Transesterification Process
Inside the plant, operators heat the clean, filtered oil to roughly 70 °C, charge it with methanol, and introduce the catalyst blend. This chemical reaction separates triglycerides, creating a heavy glycerol layer and an upper phase of new biodiesel. Before certification, the fresh fuel is washed, dried, and treated with cold‑flow additives to push the gel point low enough for cold weather starts, ensuring dependable flow through winter fuel lines.
Every step of the biodiesel production process is lab‑verified. Analysts track free fatty acids, moisture, and sulfur. Any off‑spec drum recycles until it meets ASTM D‑6751. When plants produce biodiesel to spec, fleets get a drop‑in replacement that rivals petroleum fuel on performance.
Biodiesel Production and Quality Control
Today’s biodiesel production facilities echo pharmaceutical plants: stainless reactors, inline spectrometers, and looped pH controls. Each gallon of finished fuel meets spec before it heads to blenders or backup water heater systems, running cleaner than traditional diesel and conventional diesel fuel.
Environmental Benefits
Replacing petroleum‑based diesel with biodiesel or renewable fuel slashes carbon emissions and particulates. It also diverts thousands of gallons of grease that would otherwise harden in city pipes. The Clean Fuels Alliance values these public‑health savings at roughly $7.5 billion a year once the nation replaces just ten percent of its diesel fuel with biodiesel fuel.
Economic Upside
At 30 ¢ a pound, capturing 125 gallons of fryer oil nets about $280 in monthly rebates, replacing what restaurants once paid plumbers. Regional networks of biodiesel production plants create skilled positions for welders, chemists, and CDL drivers. Nationally, the industry supports 107 000 jobs and injects $42.4 billion into GDP.
Training, Safety, and Compliance
Daily habits keep the cycle humming. Staff lock tank lids after service, track capacity sensors, and call pickups early. Managers audit manifests, ensuring every gallon moves from oil into biodiesel, not into drains. Plant crews complete refresher courses on catalyst handling, spill response, and waste‑heat recovery.
Conclusion and Outlook
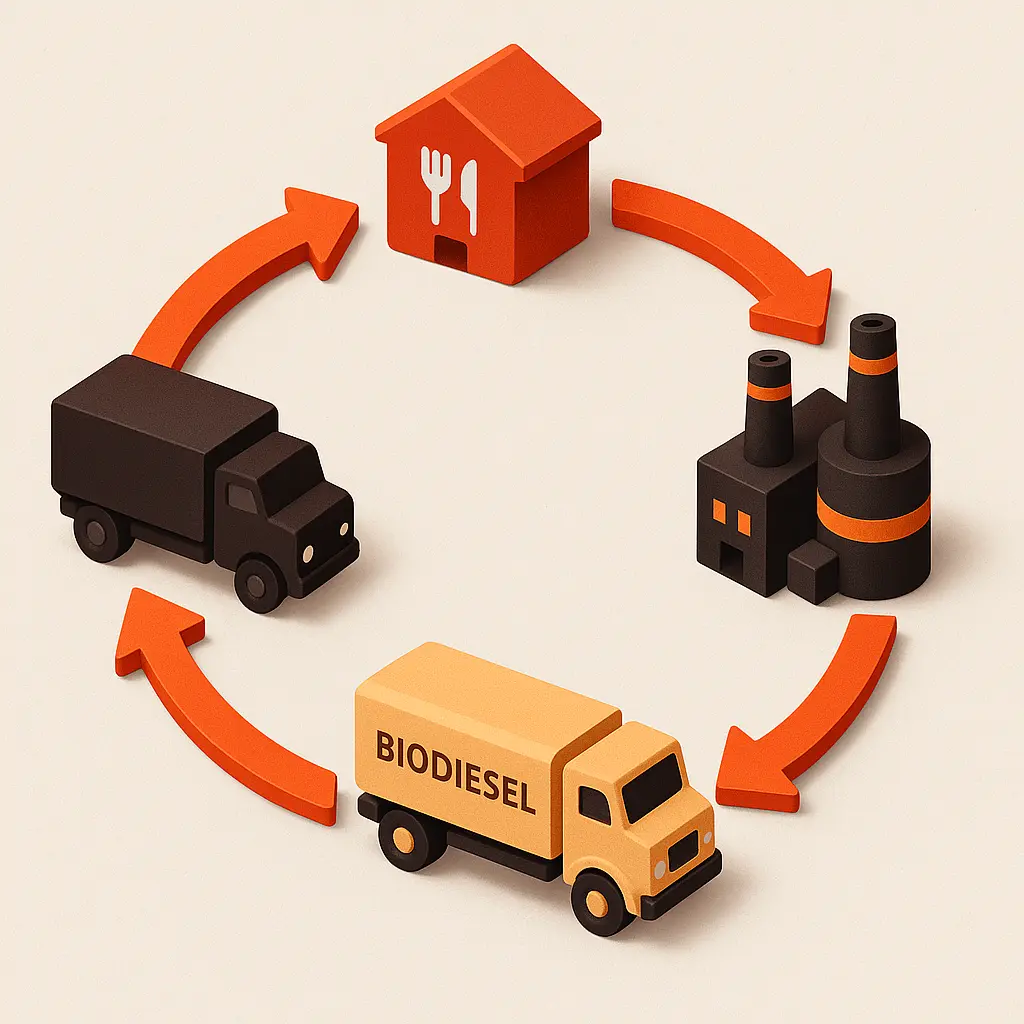
More than five billion gallons of biodiesel fuel and renewable diesel course through U.S. pipelines every year, and demand keeps rising. Continued growth hinges on robust cooking oil collection, disciplined grease trap service, and smarter reactors that produce biodiesel at higher yield. From sizzling fryers to low‑smoke exhaust, yesterday’s drippings are propelling tomorrow’s freight, trimming the climate bill one basket at a time.